Industrial companies often have large amounts of data without generating any added value from it. According to a study by the World Economics Forum in cooperation with A.T. Kearney is currently 70% of all collected production data is not used.
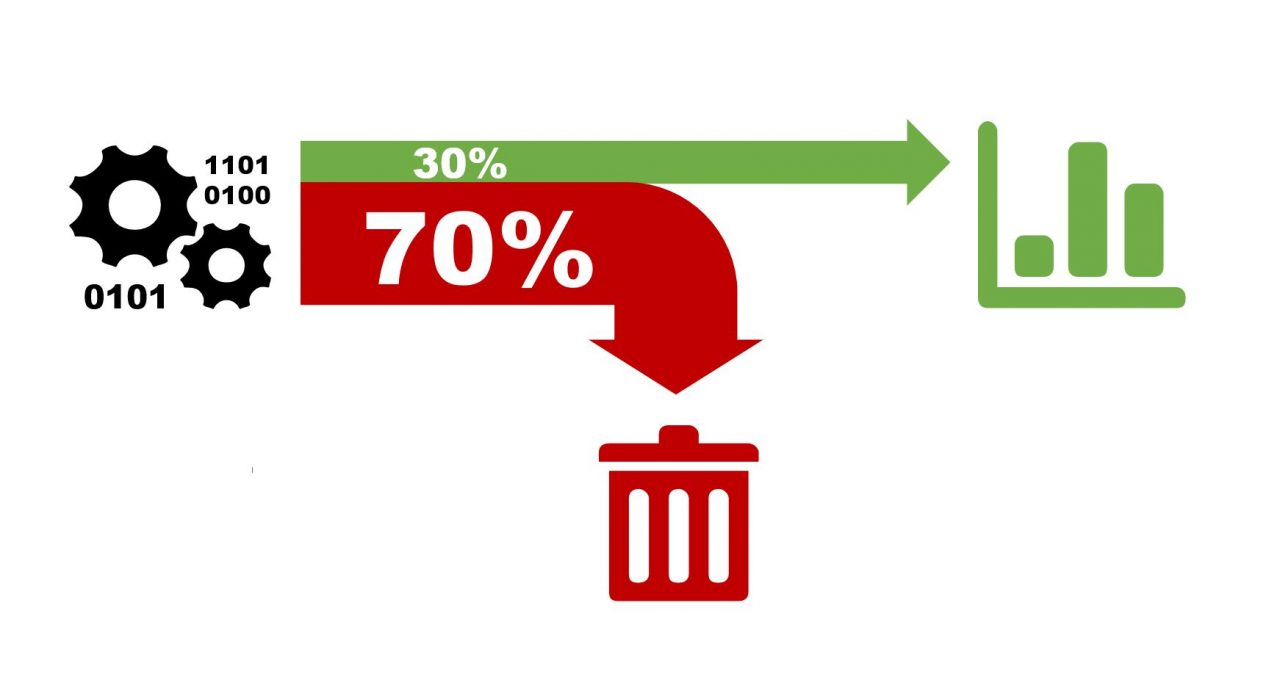
The development of market-ready AI tools and the availability of scalable computing power enable manufacturers to integrate machine learning into their processes. By using these self-learning algorithms, companies can gain proactive insights into production and thus become more competitive.
The core technologies of machine learning go well with the complex issues that manufacturers face every day. In an effort to efficiently operate supply chains to tailor made products in a timely manner, machine learning algorithms have the potential to achieve greater predictive accuracy than traditional methods at every stage of production. Many of the algorithms developed are iterative. They continuously learn to achieve consistently optimized results.
Below are three scenarios that show how machine learning can revolutionize production.
Increasing production capacity by up to 20% while reducing material consumption costs by 4%. Intelligent manufacturing systems that rely on predictive data analysis and machine learning have the potential to significantly improve machine, production, and plant-level yield rates. The following Industry 4.0 study by General Electric summarizes the benefits that can be gained through predictive analytics and machine learning in today’s manufacturing environment.
Provide relevant data so that financial, operations, and supply chain teams can better manage operational and demand constraints. In many manufacturing companies, IT systems are not sufficiently integrated. This makes it difficult for the cross-functional teams to achieve common goals. Machine learning has the potential to give these teams a whole new level of insight and intelligence into the data. This will enable teams to better optimize and redesign production processes, inventory, work-in-process (WIP), and value chain decisions. There is also a study on this. Also from General Electric.
GE Global Research Stifel 2015 Industrial Conference
Revolutionize product and service quality with machine learning algorithms that determine which factors impact most and least on company-wide quality. Manufacturers are often confronted with establishing product and service quality at the workflow level as a core component of their business. Often the quality is isolated. Machine learning optimizes product and service quality by determining which internal processes, workflows and factors contribute most to achieving the quality goals. With the use of machine learning you will be able to reach a much larger manufacturing intelligence by one can predict how their quality and procurement decisions can help, for example, to better Six Sigma performance within the DMAIC framework.
Industry 4.0 will not exist without the use of artificial intelligence or machine learning. You can say that for sure today. Businesses are now challenged to think hard about where to leverage such technology. Future competitiveness will depend largely on whether you are working with intelligent processes or are still dealing with the static or conventional processes. The latter will prove to be a decisive competitive disadvantage in the future.
In this article, we showed three ways how machine learning can revolutionize production processes. The list of possibilities could be expanded as desired. This alone speaks for the potential of machine learning.
Contact: info@aisoma.de
Your AISOMA Team
More articles about the topic:
Smart Predictive Maintenance: the Key to Industry 4.0